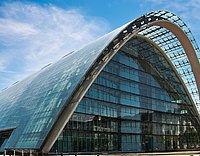
Vor allem die Kapazitäten des Lagers, in dem der Käse ungestört reift, und die Förderwege im Versandbereich stießen in Feldkirchen zunehmend an ihre Grenzen. Um gleichzeitig für weiteres Wachstum gewappnet zu sein und die künftige Wettbewerbsfähigkeit zu sichern, entschied sich Berglandmilch für eine Modernisierung. Genau hier setzt die Expertise von Körber Supply Chain Automation an. Der Geschäftsbereich ist unter anderem auf komplexe Industrie- und Logistikanlagen, Distributionszentren und Lager spezialisiert ist und hat zahlreiche Modernisierungsprojekte für Unternehmen aus den Bereichen Automobilindustrie, Maschinenbau, Pharma, E-Commerce und Nahrungsmittel begleitet.