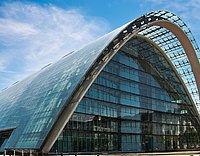
The Körber engineers and developers use different approaches, depending on the production facility and the industry. For example, Smooth Operator can increase production speed while maintaining the same high product quality. In order to do that, the AI system reads out machine data, processes this data using intelligent algorithms, and thus determines the optimal production path for each product. Experts like Kinstler call these production paths centerlines, which can be compared with the ideal line of an auto racing circuit or a ski run. These center lines are offered as recommended optimal settings to the machine operators on a smart phone or a tablet.
“Of course the way the algorithms work in detail is a trade secret — just like the recipe for a perfect sauce made by a celebrity chef,” Alexander Kinstler explains. The only thing he can reveal is that each solution is based on a mix of statistical models and AI methods such as machine learning, combined with other Körber solutions. However, it’s no secret that Smooth Operator achieves huge increases in OEE. “In one project we’ve already increased the OEE by 13 percentage points,” Alexander Kinstler says with pride. This won’t be the case with every machine and for every customer, he explains, but he expects that Smooth Operator can increase OEE by at least five to ten percentage points on average.