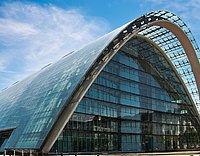
Until recently, inspection cameras were unable to distinguish between harmless air bubbles and harmful foreign bodies in syringes and ampoules. An innovation from the Körber Business Area Pharma now immediately recognizes the difference between the two, and thus offers extensive benefits to the pharmaceutical industry.
Air bubbles are a serious matter for Werner Halbinger. “I’ve declared war on them,” he says. That’s because “they cause all kinds of problems” for him as an image-processing and laboratory engineer at the Körber Business Area Pharma, not to mention the company’s customers. The Business Area Pharma offers its Seidenader Solutions high-tech machines that inspect syringes, ampoules, and vials of various sizes in order to detect foreign particles or production defects.
Different inspection techniques are used depending on the product and receptacle in question. Most of the products tested are clear liquids in transparent and colorless glass receptacles, which undergo stringent quality assurance screenings. Anything that throws a shadow could be a foreign body but that doesn’t necessarily have to be the case. “Unfortunately, air bubbles are also registered as shadows by the detectors,” Halbinger explains. Such bubbles used to present a major challenge to Halbinger, his colleagues, and customers throughout the entire pharmaceutical industry.